Department Focus—Measure Twice, Cut Once
- J.Anthony Tedpahogo
- Aug 9, 2024
- 3 min read
Manson’s Production Engineering Group consists of a highly capable team of engineers providing back-end and front-end support to nationwide marine construction and dredging projects.
“Production engineers help determine how long a project will take based on our production rates,” says Vice President & Chief Engineer of Dredging Mike Warwick. “They look at several things, like the site material and equipment, and then utilize theoretical models to make calculations. The group gives that information to the estimators, who figure out how much everything will cost.”
A crucial foundation for the estimating, planning, and operations phases, the Production Engineering group’s work is divided among five members, led by Production Manager Connor Tennant with oversight from Mike.

Most of the team’s work relies heavily on implementing historical data from both marine construction and dredging projects, but their work extends to geotechnical analysis (collecting soil samples from natural formations), sequence drawings, and managing and developing production databases that are used on current project sites for future Manson civil and dredging estimates.
“A big percentage of our work boils down to taking qualitative research and applying engineering sciences to produce the appropriate production rates for projects,” Connor explains. “Our work also involves visiting ongoing jobsites to ensure our project teams are executing the work efficiently.”
Applying Production Engineering to the Work
When a marine construction or dredging project crosses the estimating team’s desk, a member of the Production Engineering group is alerted to prepare a means and methods summary and gather production rates for activities.
“During the estimating phase, we look at similar past projects, available equipment, soil conditions, and measure activities in a step-by-step process for further analysis,” says Production Engineer Nathaniel “Nate” Vazquez.

A common production engineering practice useful to estimators is breaking down the work activities. Using in-house historical databases, the group can break down a variety of activities, including but not limited to selecting diesel hammers and examining their capabilities, analyzing loading cycles for dredge buckets, testing transportation of material by scows and tugs, and performing winch-line pulls.
“The historical database is a useful tool that provides insights for better understanding of how projects operate and shaving off percentages to make the work more efficient,” explains Production Engineer Joe Hannon. “Austin [Idle, Production Engineer] and I manage the software with a goal of making the data accurate, accessible, and on par with the industry.”
With no shortage of software and data accurately depicting how project teams can execute the work, the group’s resources go beyond the computer screen, with access to an in-house geotechnical lab. Equipped with tools to examine soil mechanics, the team can develop a better understanding of the material. Using an in-house lab eliminates the need for a third-party to gather data while allowing the group to archive information for future use.
“We look at soil conditions and utilize programs to help plan projects and how we can perform dredge work at similar sites,” Austin says. “The main goals for this group are to assist the estimating department with winning new projects and to ensure our equipment is operating as efficiently as possible.”
When the Magic Happens
The Production Engineering group’s work is the embodiment of the adage, “Measure twice and cut once.” The group provides project teams with proven methods to optimize production through accurate data, but there are moments when the group must show flexibility should the data change.

“If material at a project site differs from the historical data, the group has no problem acclimating to the situation,” Mike says. “They are knowledgeable enough to know what engineering steps to apply to generate accurate production rates. That is when the real magic happens.”
If the group needs to investigate material that differs from comparable sites, one or two members of the team are deployed to collect soil samples.
“We will conduct some field exploration and take borings in different areas at the project location,” Connor explains. “We will take the samples, test them, and digitize the data for project use.”
Helping Project Teams and Crews Do the Work
While the group has proven its expertise, a common set of interests among the team members is curiosity and continued learning. Visiting project sites and establishing relationships with the project teams and crews in the field affords them the opportunities to continually improve their work product.
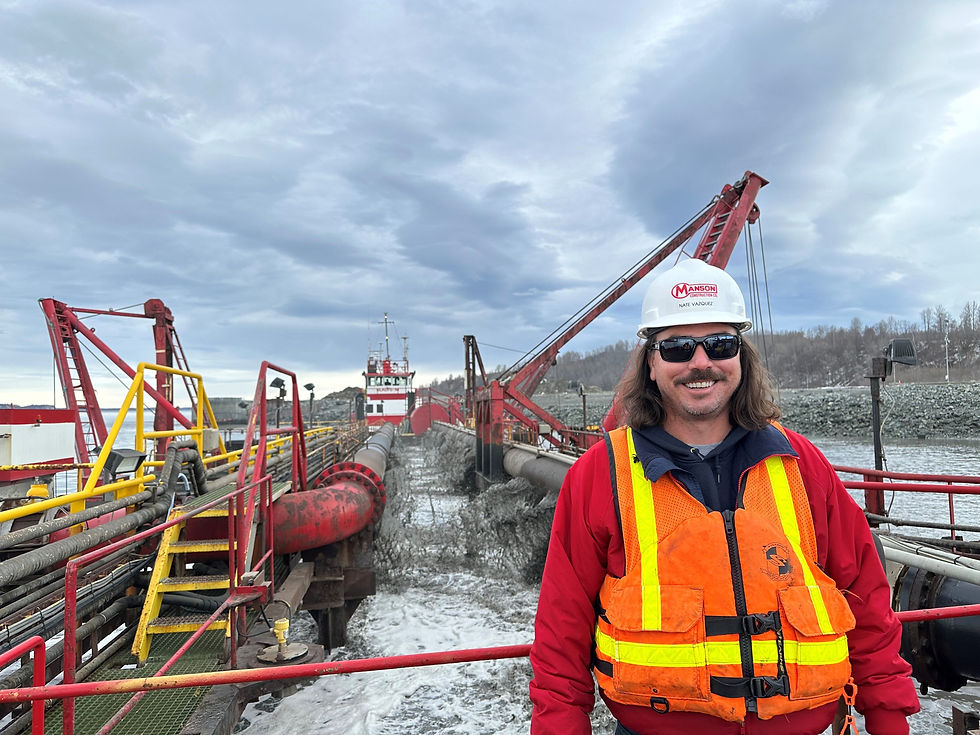
“One of the most valuable things about hanging out with the crews is that you get to learn about their knowledge of the project and equipment,” Nate says.
During these visits, they learn more details about how the project crews approach the work and their experiences.
“We can then take that data and turn around and apply that to production,” he says, “which helps us to complete projects on time and keep the crews working safely and efficiently.”
Comments